10 ways in which manufacturers can reduce their Carbon (GHG) emissions
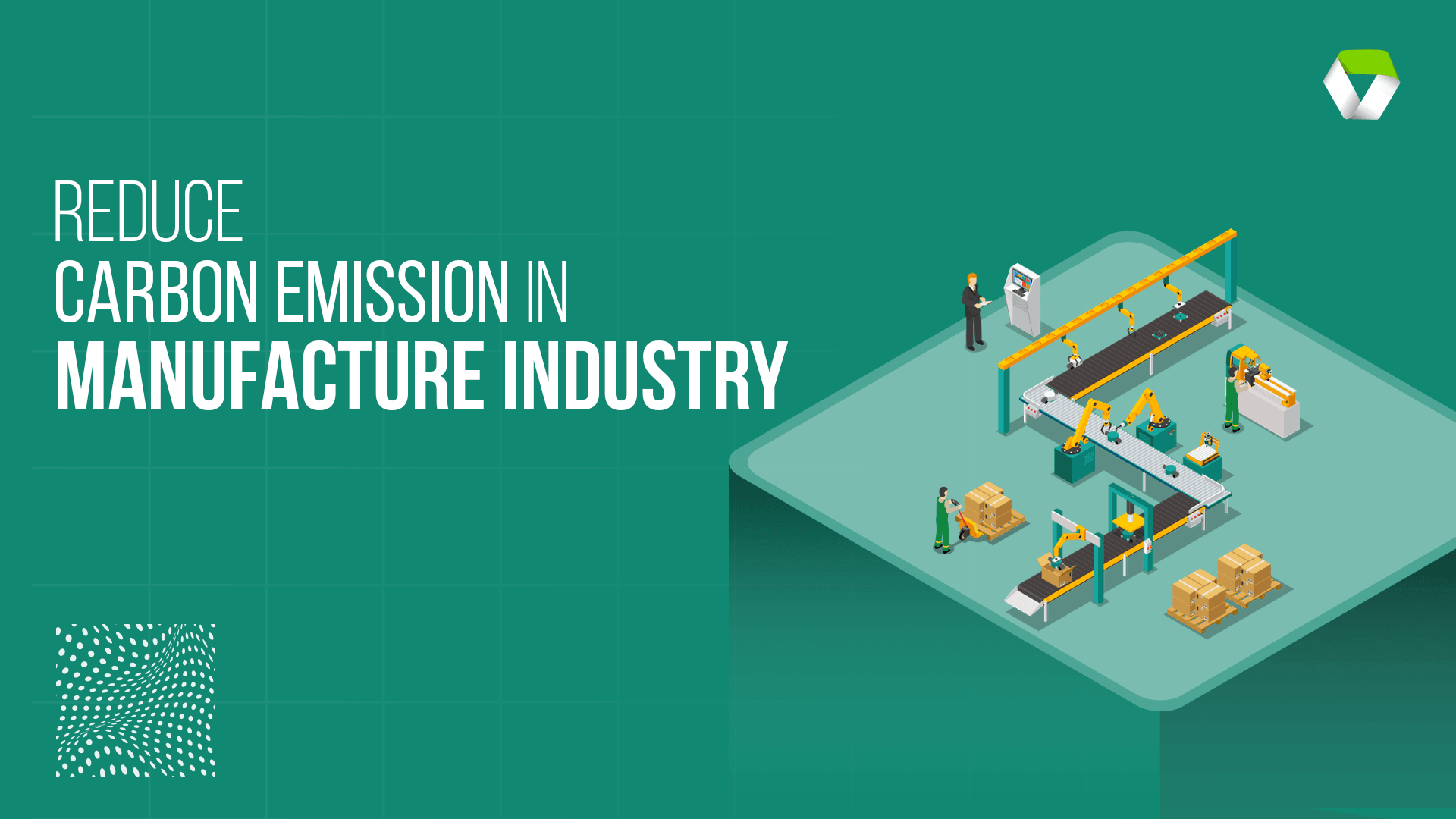
A quarter (23%) of direct emissions in the US is contributed by manufacturing alone. Manufacturing is a major contributor to global Greenhouse gas (GHG) emissions and represents a significant challenge to sustainability goals. This calls for a paradigm shift. Manufacturers must prioritize sustainability, not just as a buzzword, but as a core principle.
Why does sustainability matter for manufacturers?
Climate change is no longer a distant threat; it’s an immediate concern with far-reaching consequences. Rising global temperatures disrupt supply chains, lead to extreme weather events, and threaten the very resources needed for production. Beyond the environmental imperative, there’s a compelling economic case for sustainability. Consumers are increasingly making purchasing decisions based on a company’s environmental practices. Moreover, regulations around carbon emissions are becoming stricter, making it costly for manufacturers to remain non-compliant.
Understanding the manufacturing Carbon footprint
Before diving into solutions, it's crucial to understand where emissions originate within a manufacturing process. The carbon footprint of a manufacturing operation typically comprises three scopes:
- Scope 1: Direct emissions from owned or controlled sources, such as on-site fuel combustion.
- Scope 2: Indirect emissions from purchased energy, like electricity and heat.
- Scope 3: Indirect emissions from the value chain, including transportation, raw material production, and product use.
10 strategies for manufacturers to reduce Carbon (GHG) emissions
Manufacturers can create a greener future by taking the right steps. This involves adopting a multi-pronged approach that prioritizes resource efficiency, embraces circular economy principles, and leverages cutting-edge technologies. Here are 10 key strategies for manufacturers to significantly reduce their carbon footprint:
1.Embrace the Circular economy: Reduce, Reuse, Recycle
The traditional "take-make-waste" model is no longer sustainable. The circular economy offers a solution. It emphasizes maximizing resource use throughout a product's lifecycle by focusing on:
- Reduce: Design products that are durable, easy to repair, and require minimal materials. Studies have shown that a 10% reduction in material use can lead to a 5-6% reduction in a product's carbon footprint.
- Reuse: Find new life for existing components through remanufacturing, refurbishment, or disassembly of spare parts. Volvo Group, for example, remanufactured used parts for new vehicles, achieving an 80% reduction in energy consumption compared to manufacturing from scratch.
- Recycle: Integrate recycled materials like steel into production processes. The Environmental Protection Agency (EPA) estimates that secondary steel production uses about 74% less energy than virgin steel.
2. Champion sustainable material sourcing
Partner with suppliers who prioritize responsible resource management and utilize recycled materials. Evaluating suppliers' carbon footprints, encouraging sustainable practices, and collaborating in carbon reduction initiatives minimize the environmental impact of material extraction and processing.
3. Leverage technology for efficiency and optimization
Technological advancements offer exciting possibilities for sustainable manufacturing:
- Artificial Intelligence (AI): AI-powered processes can optimize production lines, minimize waste, and identify areas for energy efficiency improvements.
- Additive manufacturing (3D Printing): 3D printing allows for on-demand production, reducing excess inventory and minimizing transportation emissions associated with traditional manufacturing methods.
- Smart manufacturing: Utilizing sensors and data analytics to monitor energy consumption in real time allows for targeted interventions and energy-saving strategies.
- Carbon Capture and Storage (CCS): For industries with high emissions, CCS can capture and store carbon dioxide before it enters the atmosphere.
4. Monitor and reduce energy consumption
Regularly assess energy use throughout the manufacturing process. Identify areas for improvement and implement targeted energy-saving strategies, such as upgrading equipment to more energy-efficient models.
Explore the use of renewable energy sources like solar or wind power to reduce reliance on fossil fuels. According to the International Renewable Energy Agency (IRENA), the global manufacturing sector has the potential to reduce its energy consumption by 34% by 2050 through energy efficiency measures and a shift to renewable energy.
5. Prioritize water conservation
Implement water-efficient practices throughout the manufacturing process. This may involve upgrading equipment, recycling water where possible, and identifying and eliminating leaks.
6. Minimize waste generation
Streamline production processes to minimize waste generation. This can involve optimizing material usage and exploring ways to reuse or recycle scrap materials. Implement responsible waste disposal practices to minimize environmental impact.
7. Design for sustainability
Products designed for disassembly, repair, and extended lifespan contribute significantly to a circular economy. Consider these factors during the design phase:
- Use durable and easily repairable materials.
- Design products that can be easily disassembled for component reuse or recycling.
- Consider the potential for product upgrades or extensions of lifespan through modular design.
8. Foster a culture of sustainability
Employee engagement is crucial for successful sustainability initiatives. Educate employees about the environmental impact of manufacturing and empower them to identify and implement sustainable practices in their daily work.
9. Partner with Policymakers
Advocate for policies that incentivize sustainable practices and promote renewable energy sources. Collaboration between industry and policymakers can create a more supportive environment for green manufacturing.
10. Encourage transparency: Monitor and disclose
Transparency is key to achieving meaningful progress in sustainability. Manufacturers need to establish robust monitoring and disclosure practices to effectively track their environmental impact. This includes:
- Comprehensive emissions monitoring: Regularly measure and record greenhouse gas emissions across all stages of production, providing a clear picture of the company's environmental footprint.
- Resource utilization analysis: Track resource consumption, including water usage and raw materials, to identify areas for optimization and waste minimization.
- Transparent reporting: Regularly publish sustainability reports that disclose environmental data and progress toward sustainability goals. This helps build trust with stakeholders and demonstrates your commitment to environmental responsibility.
Sustainium’s innovative carbon accounting platform helps manufacturers track, report, and reduce their emissions.
Making a business case for green manufacturing
Transitioning to a sustainable manufacturing model requires upfront investment but it has long-term benefits. In addition to achieving net-zero goals, going green can help manufacturers gain financial benefits and a competitive edge. So, here are three points to consider when transitioning to sustainable manufacturing.
- Cost savings: While initial investments may be required, resource efficiency upgrades and new technologies can lead to substantial long-term cost savings. Reduced waste disposal costs, lower energy consumption, and potential tax breaks for sustainable practices can significantly improve the bottom line.
- Carbon pricing initiatives: As carbon pricing mechanisms, such as carbon taxes or emissions trading schemes, become more prevalent, early adopters of sustainable practices will be better positioned to navigate the changing landscape. By reducing their carbon footprint, manufacturers can minimize the financial impact of these regulations.
- Demonstrating ROI (Return on Investment): Quantifying the return on investment for sustainability initiatives can be crucial when seeking internal buy-in from stakeholders. Highlight the long-term cost savings, potential revenue growth from a more sustainable brand image, and reduced regulatory risks associated with proactive environmental practices.
Sustainable manufacturing for a sustainable future
The transition to a sustainable future for manufacturing is crucial in building a sustainable future. Manufacturers who embrace the principles outlined above – prioritizing resource efficiency, implementing circular economy practices, leveraging technology, and collaborating across the supply chain – will be the leaders of this transformation. The journey towards a greener future for manufacturing offers great rewards – a healthier planet, a more resilient economy, and a competitive edge, making it a priority for eco-conscious manufacturers to be the champions of sustainability.
Track, report, evaluate, reduce, and manage your Carbon emissions with Sustainium. Talk to us.